DOBOT COBOT CR3S
Collaborative industrial robot arm with SafeSkin accessory
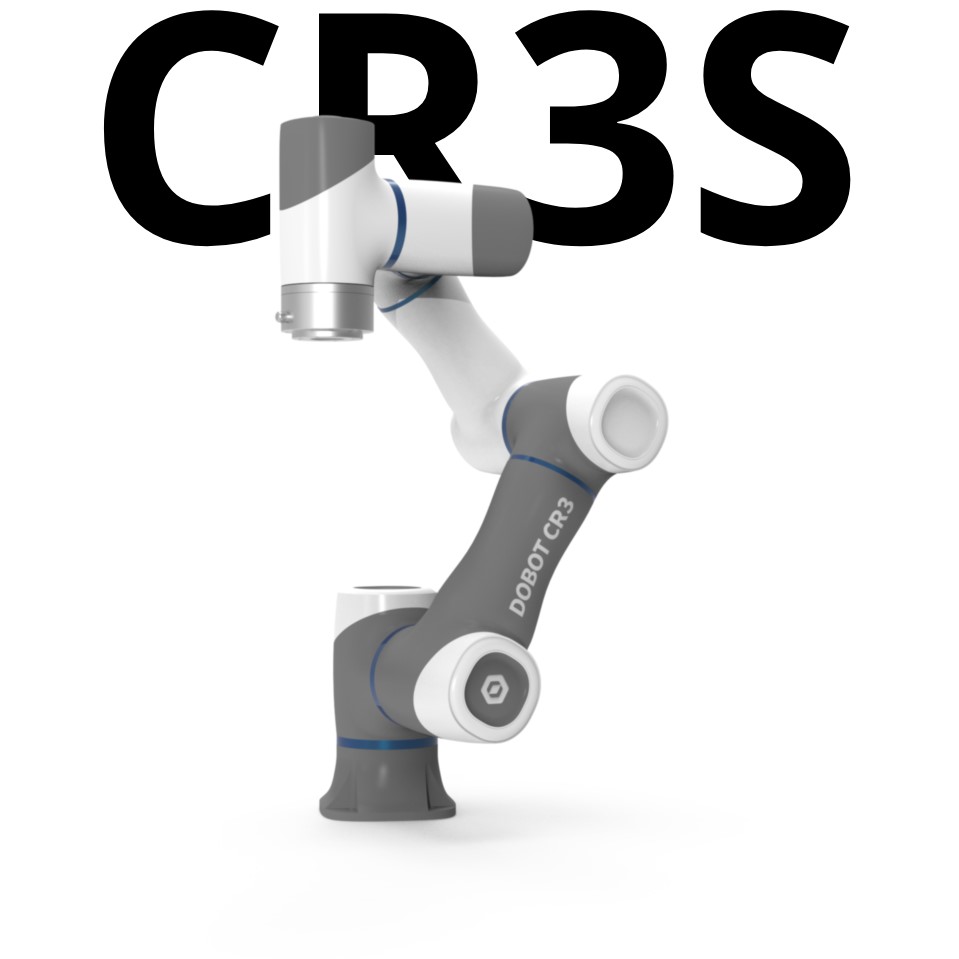
CR3S is the key to safe human-robot collaboration. Designed with the DOBOT SafeSkin add-on, the CR3S robotic arm is designed to simplify automation lines and provide a high level of safety for humans.
FLEXIBLE INSTALLATION, FAST IMPLEMENTATION
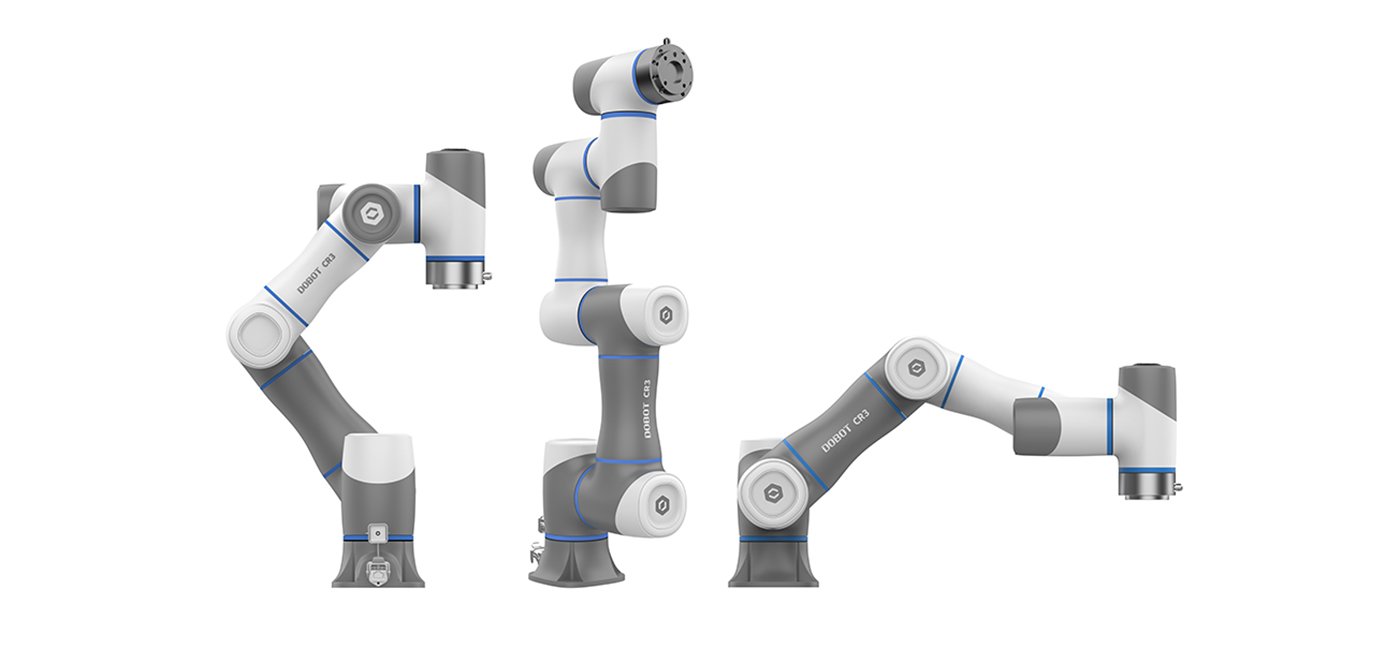
Improve workflow flexibility and production efficiency with an easy-to-deploy CR collaborative robot that can be set up in just 20 minutes and up and running in up to 1 hour. After connecting the control console and attaching the robot arm, all you need to do is connect the two devices and switch on the system.
EASY TO ACCESS, EASY TO LEARN
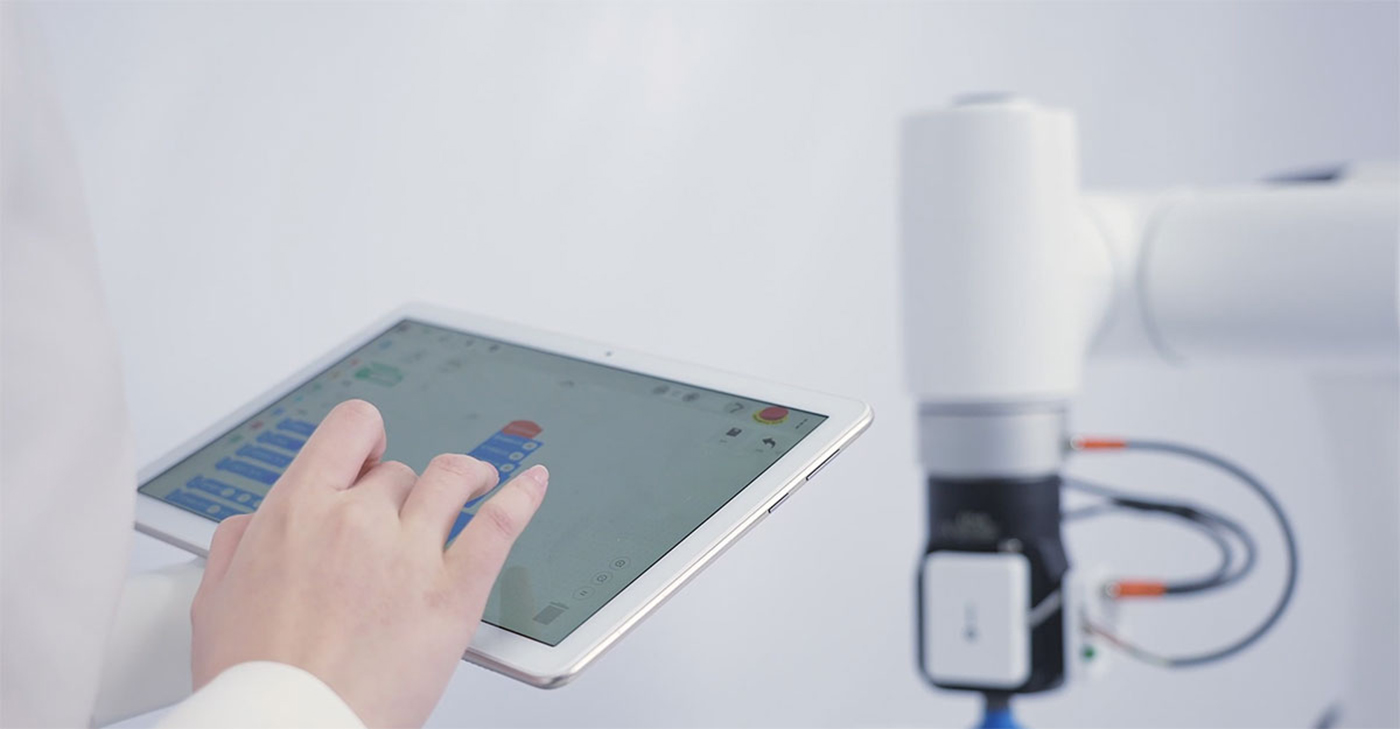
Dobot's software and arithmetic technology make the CR series of collaborative robots smart and easy to operate and manage. Thanks to software and manual training, it can accurately mimic human movements. No programming skills are required. This is facilitated by its block-based development environment, which eliminates the need to learn to use complex programming library systems and functions.
In case you have prior programming knowledge, the robot system supports the Python programming language, so you can take full advantage of the robot.
SafeSkin technology - Harnessing electromagnetic induction
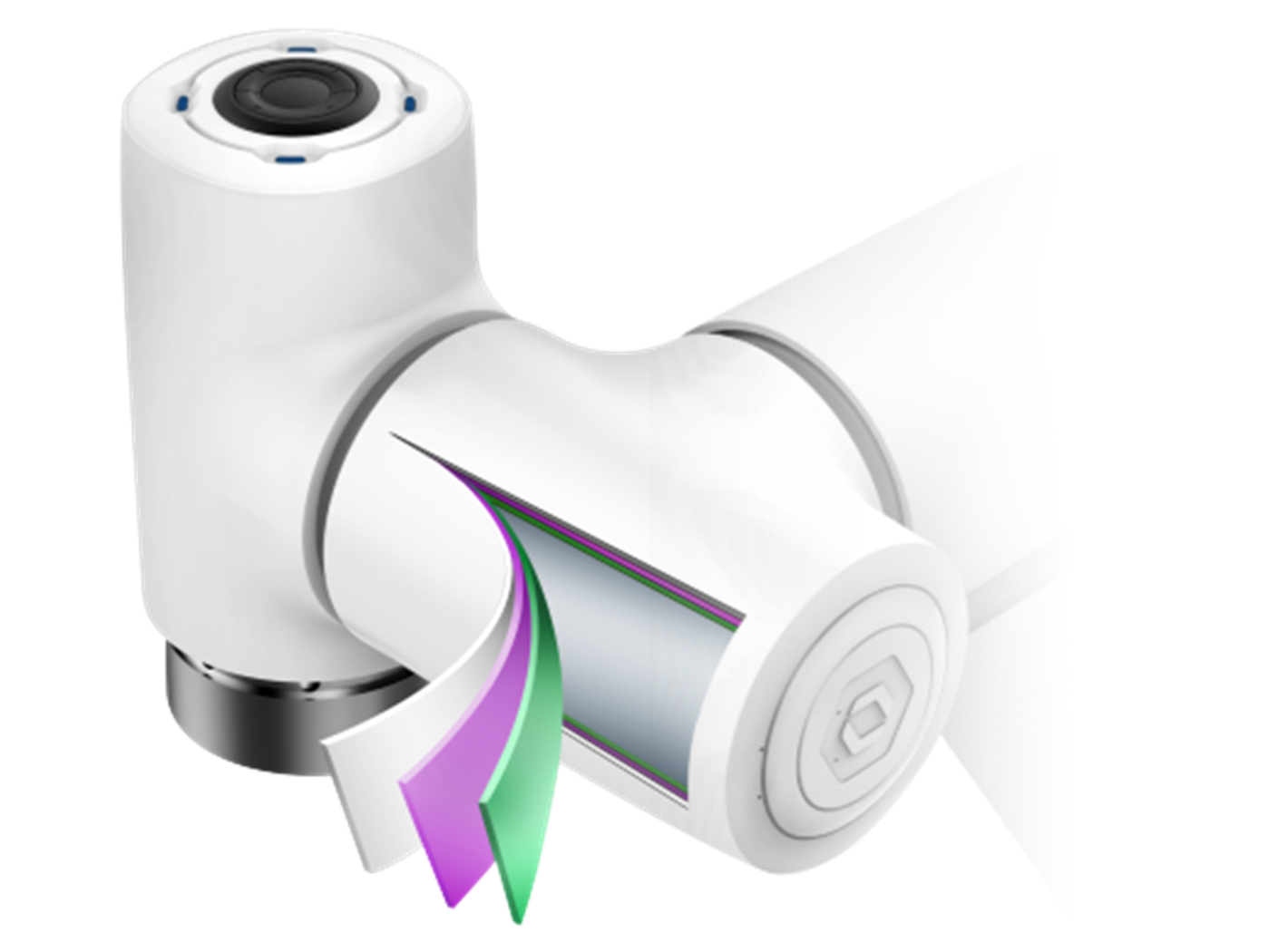
DOBOT is a proprietary safety development that allows the robotic arm not only to prevent accidents, but also to avoid them. Using electromagnetic induction, a silicone cover with sensors ensures the robot is aware of its surroundings. The envelope creates an electromagnetic field along the robot's envelope, which is refracted by any foreign object in its environment or moving around it, causing the sensor to send a signal to the robot's central processing unit. This causes the robot to stop immediately.
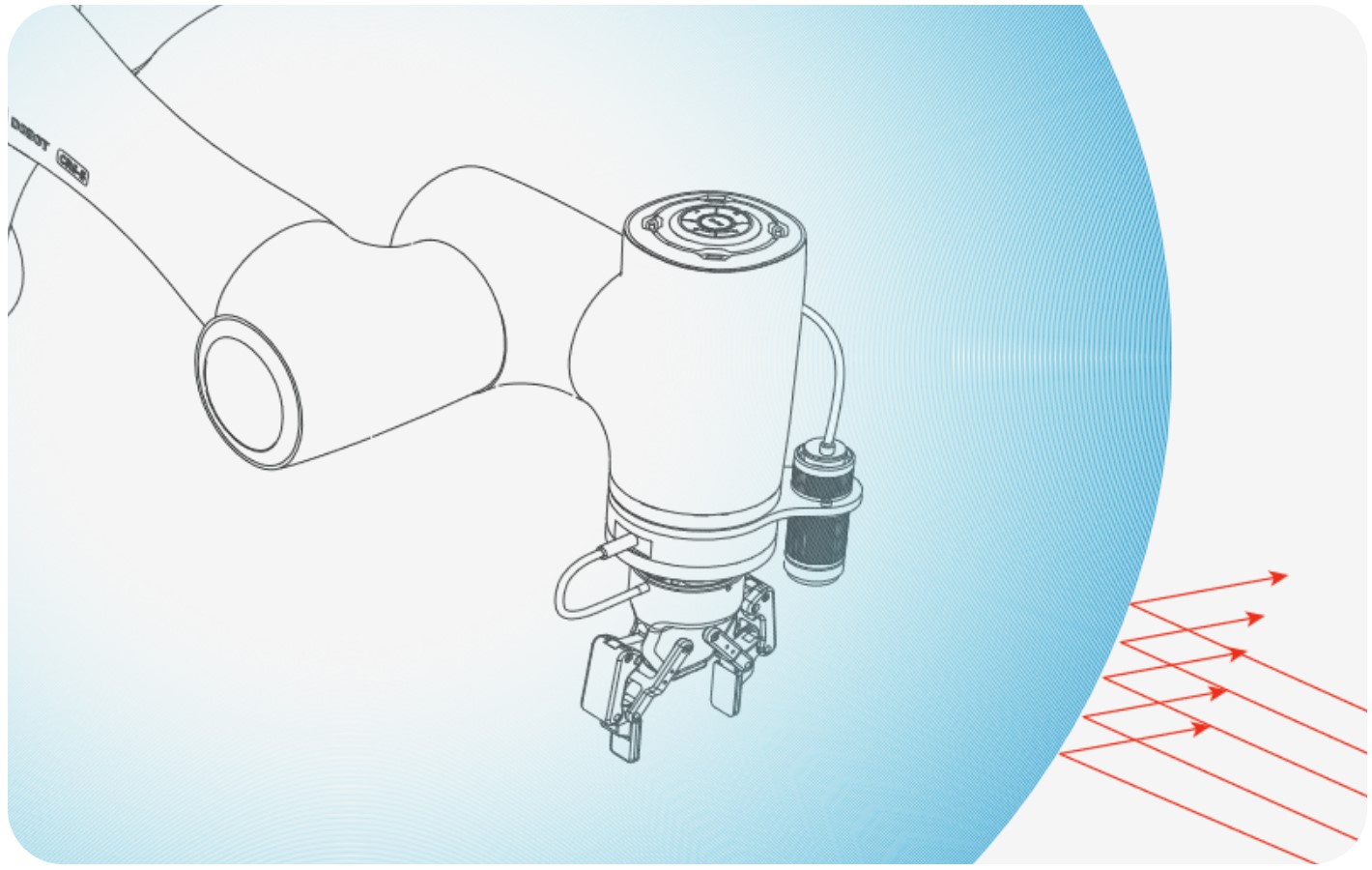
Its operation is suspended until the integrity of the magnetic field is restored, i.e. until the foreign object leaves the robot's immediate environment. Once its path of operation is free again, the robot automatically resumes its work without endangering the production process.
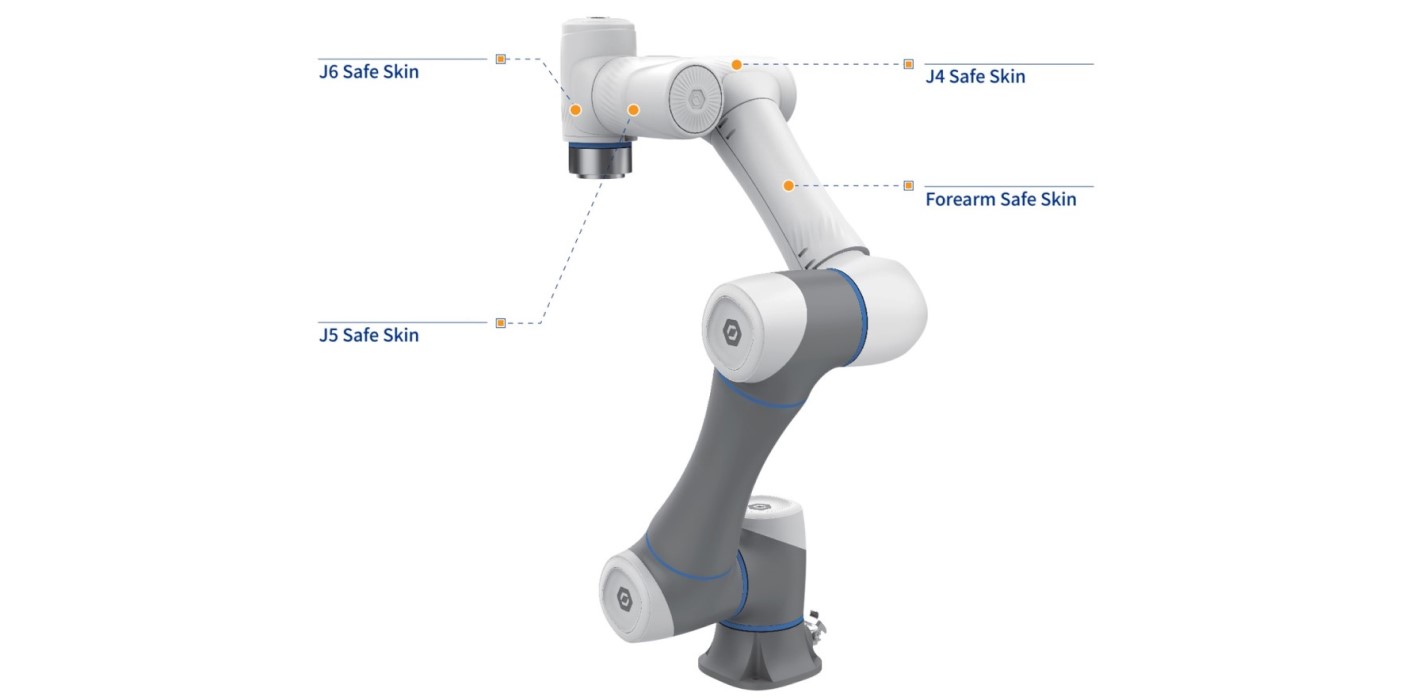
The SafeSkin package includes 4 units of cover. The forearm cover, the J4 wrist cover, the J5 wrist cover and the J6 wrist cover.
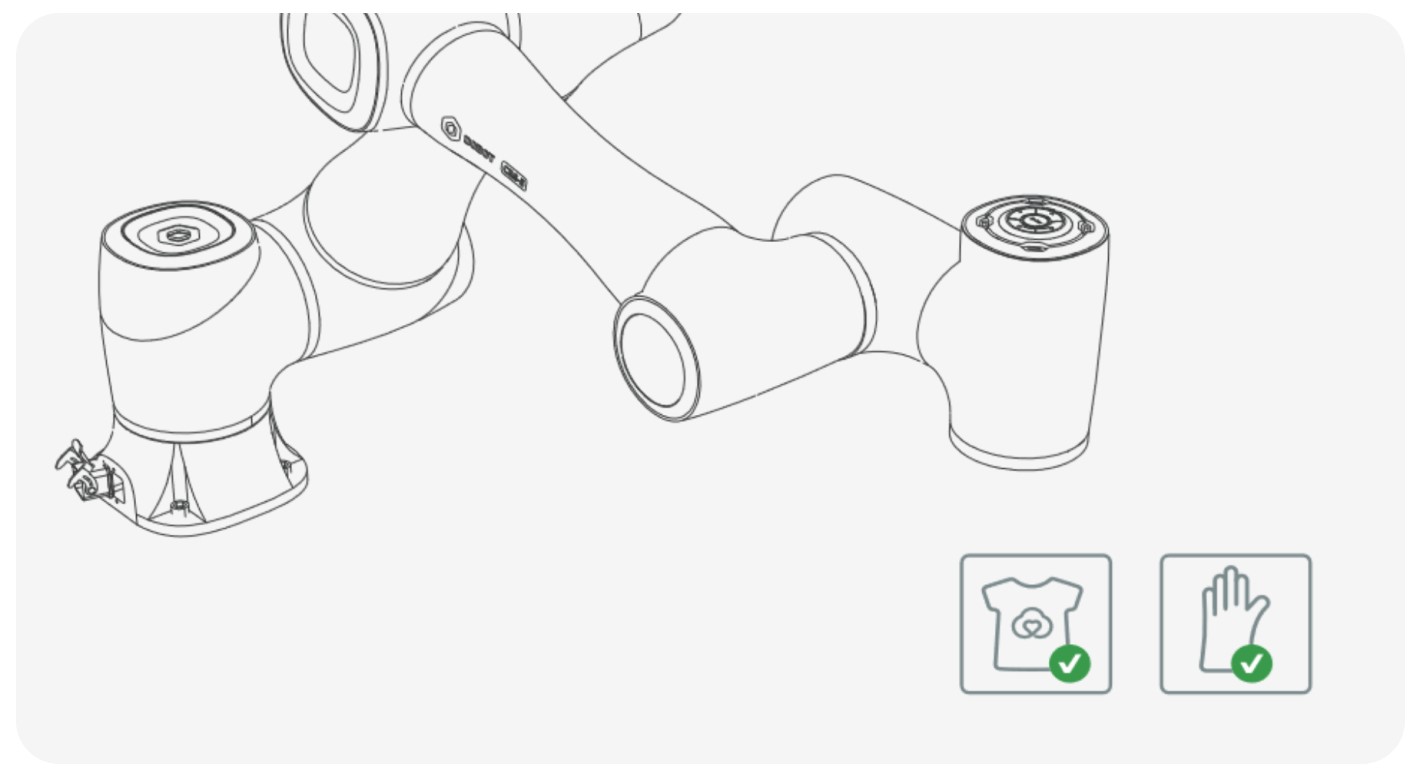
Sensitivity also varies according to the different materials. While human skin is at the highest level (coverings are the most sensitive), plastic is the lowest. Parameters related to prevention, such as acceleration and speed, can be set in the robot's development software.
Secure investment, outstanding reliability
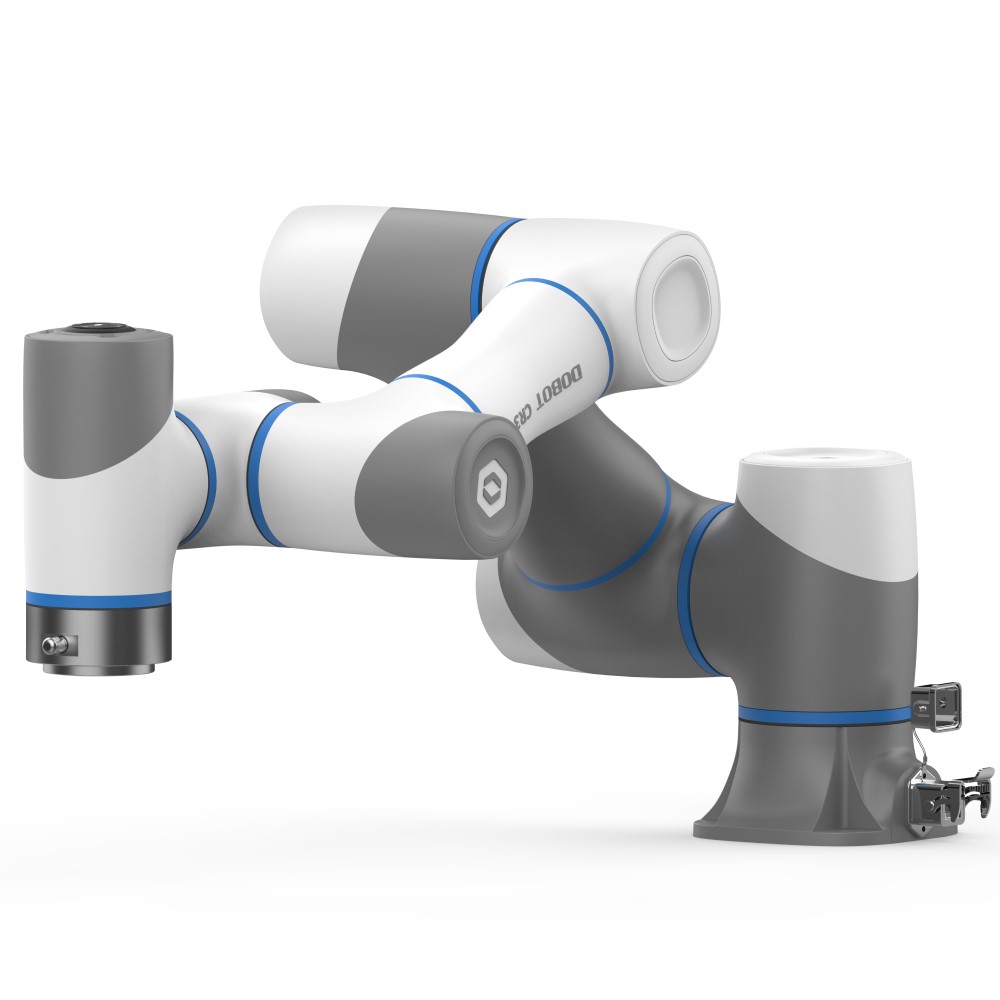
The robust and stable build quality of the CR series of collaborative robotic arms promises a lifetime of up to 32,000 hours, combined with low running costs, making the CR series not only a safe investment, but also a return on investment.
Key features:
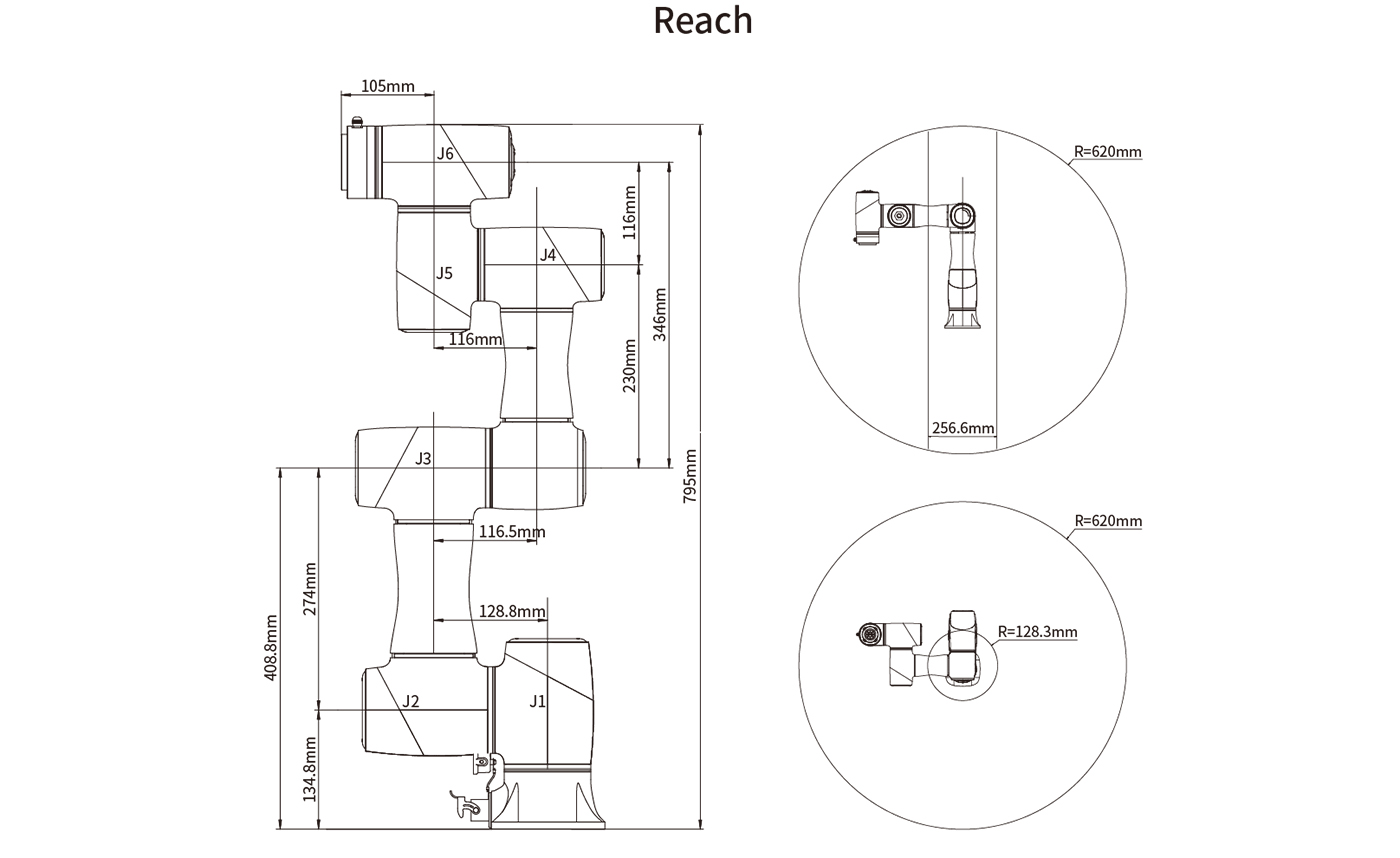
Product Name | DOBOT CR3S |
Weight | 16.5kg |
Max Payload | 3kg |
Max Working Radius | 620mm |
Rated voltage | DC48V |
Max speed of End-Tool (TCP) | 2m/s |
Range of Joints | J1 | ±360° |
J2 | ±360° | |
J3 | ±155° | |
J4 | ±360° | |
J5 | ±360° | |
J6 | ±360° | |
Max Speed of Joints | J1/J2 | 180°/s |
J3/J4/J5/J6 | 180°/s | |
End-Tool I/O interface | DI/DO/AI | 2 |
AO | 0 | |
Communication interface | Communication | RS485 |
Controller I/O | DI | 16 |
DO/DI | 16 | |
AI/AO | 2 | |
ABZ Incremental Encoder | 1 | |
Repeated Accuracy | ±0.02mm | |
Communication | TCP/IP, Modbus, EtherCAT,WIFI | |
IP Rating | IP54 | |
Working Temperature | 0~45° | |
Power | 120W | |
Materials | Aluminum alloy, ABS plastic | |
End-Tools
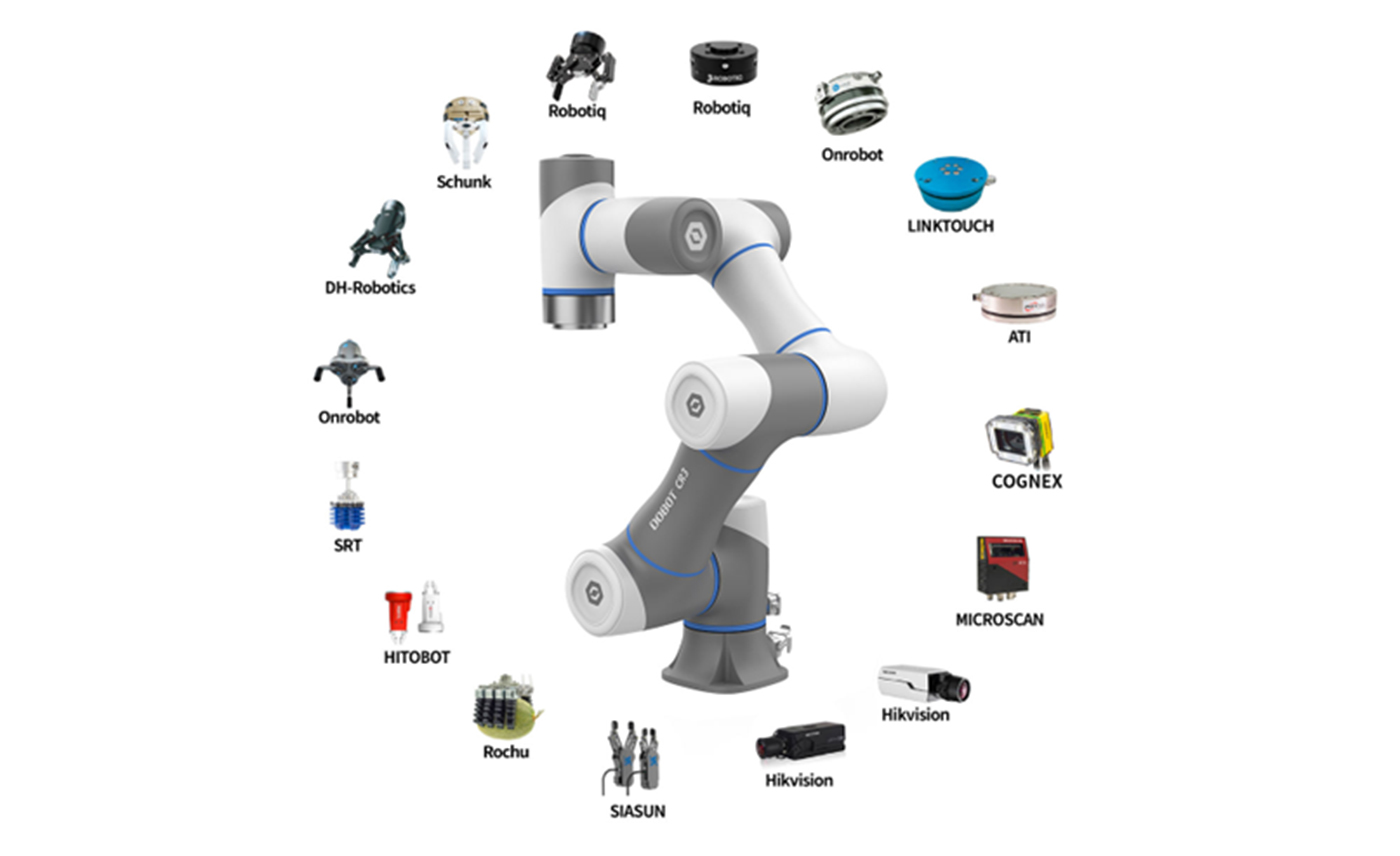
The end tools are the devices that can be mounted on the ends of the robot arms. The DOBOT CR collaborative robot series is compatible with a wide range of end tools, so it will be able to meet even the most specific needs of your business. Whether it's welding, palletising, loading, bolting, sorting, assembly or quality control, any process can be equipped with vacuum or electronically powered grippers, MODBUS units for communication and automation, or conveyor and visual unit accessories to maximise the robot arm's efficiency, such as:
- Packing and palletising
- Handling
- Polishing
- Screwing
- Gluing, batching and welding
- Assembly
- Machining
- CNC
- Quality control
- Injection moulding
Package contents
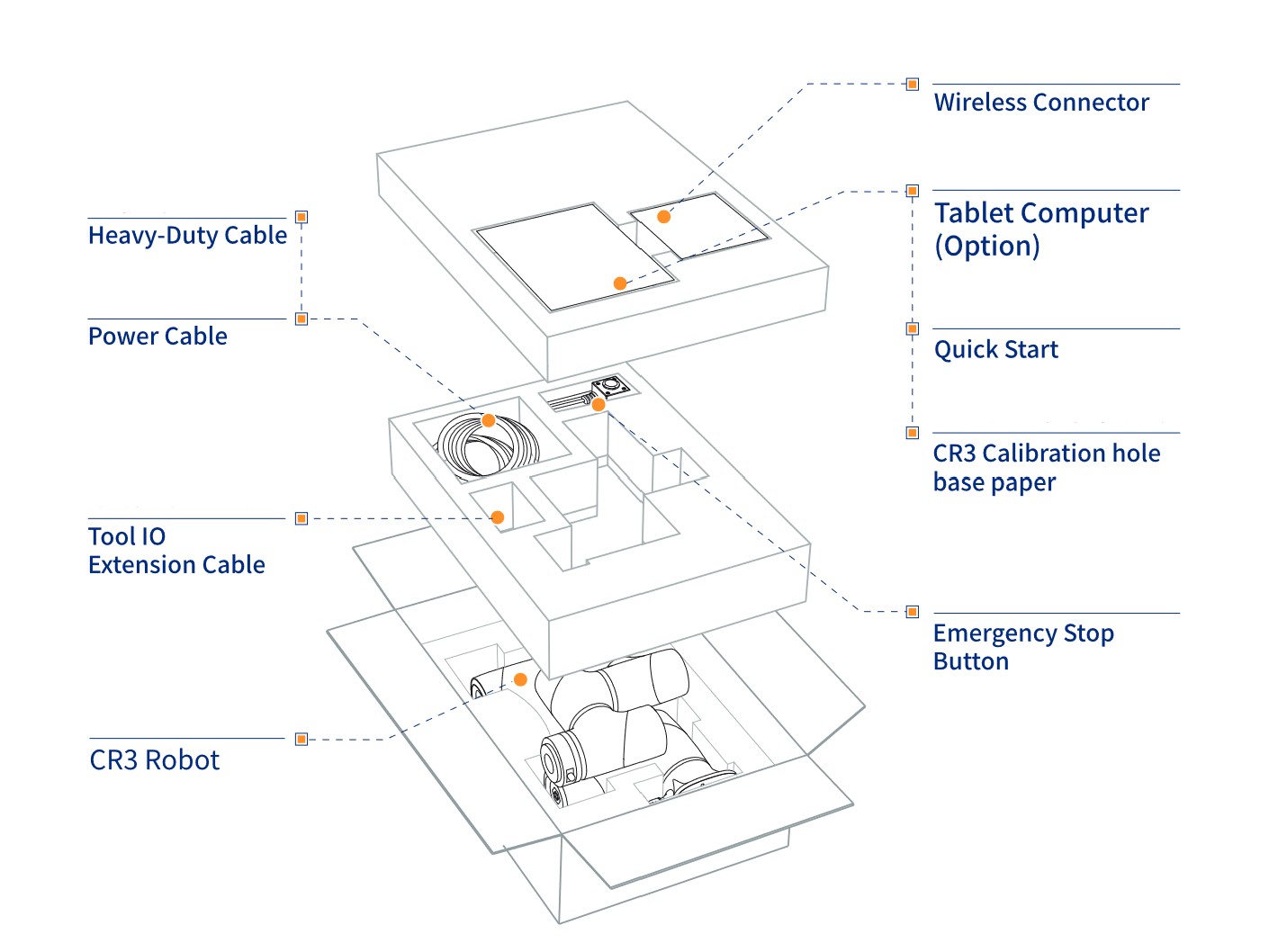
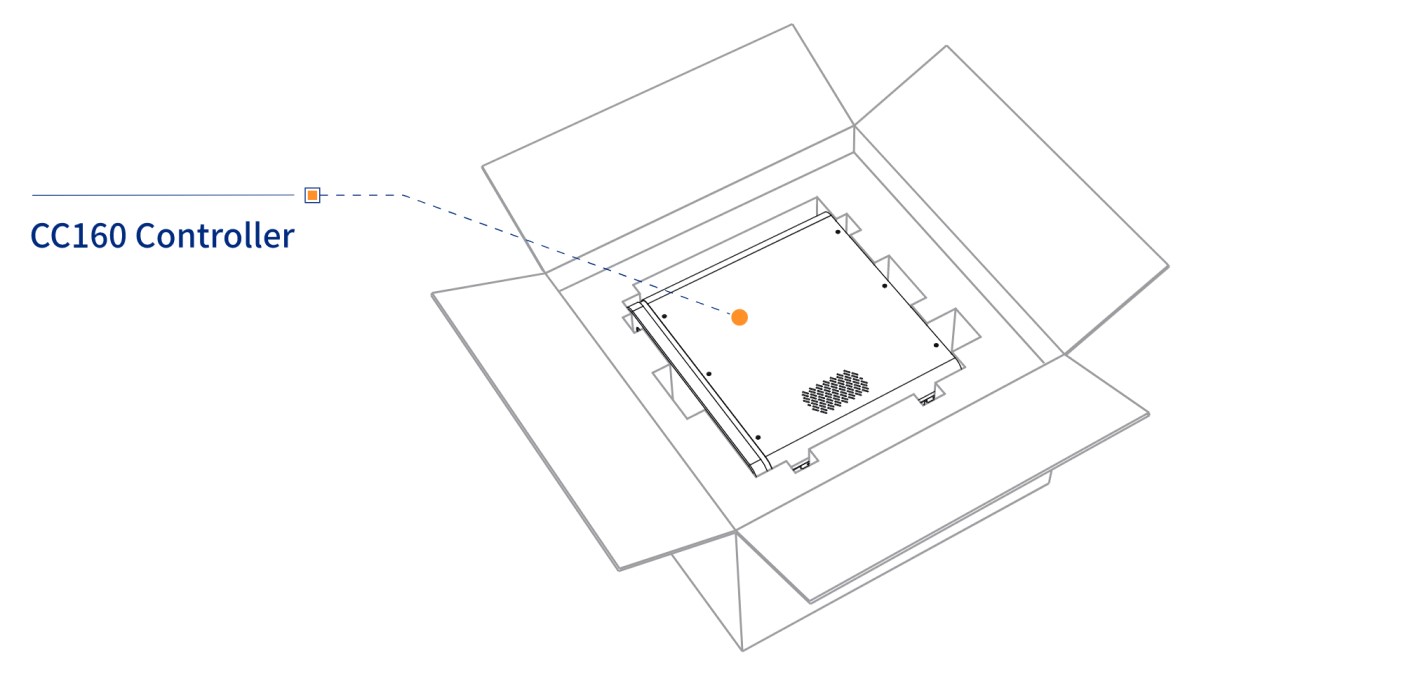
The robot arm consists of two units. A robot arm and a control unit for programming it. The control unit is a computer that communicates with the robotic arm to control it. The controller has the IO ports to which the various accessories can be connected, including the emergency stop switch. To establish communication with your computer or smart device, the controller has a USB port to which the WIFI module can be connected, and an Ethernet port if you want to control and program your robotic arm via a wired connection.
* Pressing the emergency stop switch will stop the robot immediately.
In addition to the two units, the package contains the power cables for the units and the IO cable for the connection.
The SafeSkin accessory is also included!
Programming can be done in several ways. Examples include:
Reproduction of end-tool motion: A related programming method is Teach & Playback programming, a way of programming robot arms that does not require programming knowledge to set the parameters of a task. The programmer can freely move the robot arm by pressing and holding a safety lock release button, and then release the button to stabilize the arm in the position. In the programming interface, these coordinates can be viewed and stored as a coordinate point that the robot arm must touch during the execution of a task. By saving the points, you can then move the robot arm without any programming skills.
Block-based programming (Drag and Drop): Also known as graphical programming, which makes it easier to learn programming by visualising functions, variables and modes of operation. The principle of operation is based on the linking of blocks, i.e. the blocks representing each function can be programmed in sequence to program the robot arm.
Python Script: nowadays, Python is one of the most popular programming languages and the first choice of all beginners.With its easy-to-understand syntax and large library, it is used not only for automation but also for building artificial intelligence. Thus, robotics has also chosen Python to maximise the capabilities of robots.
DobotStudio, the development environment for the robot arm, comes with the libraries needed to control the robot arm by default, so all you have to do is review the documentation and create your own Python program to run your robot arm.
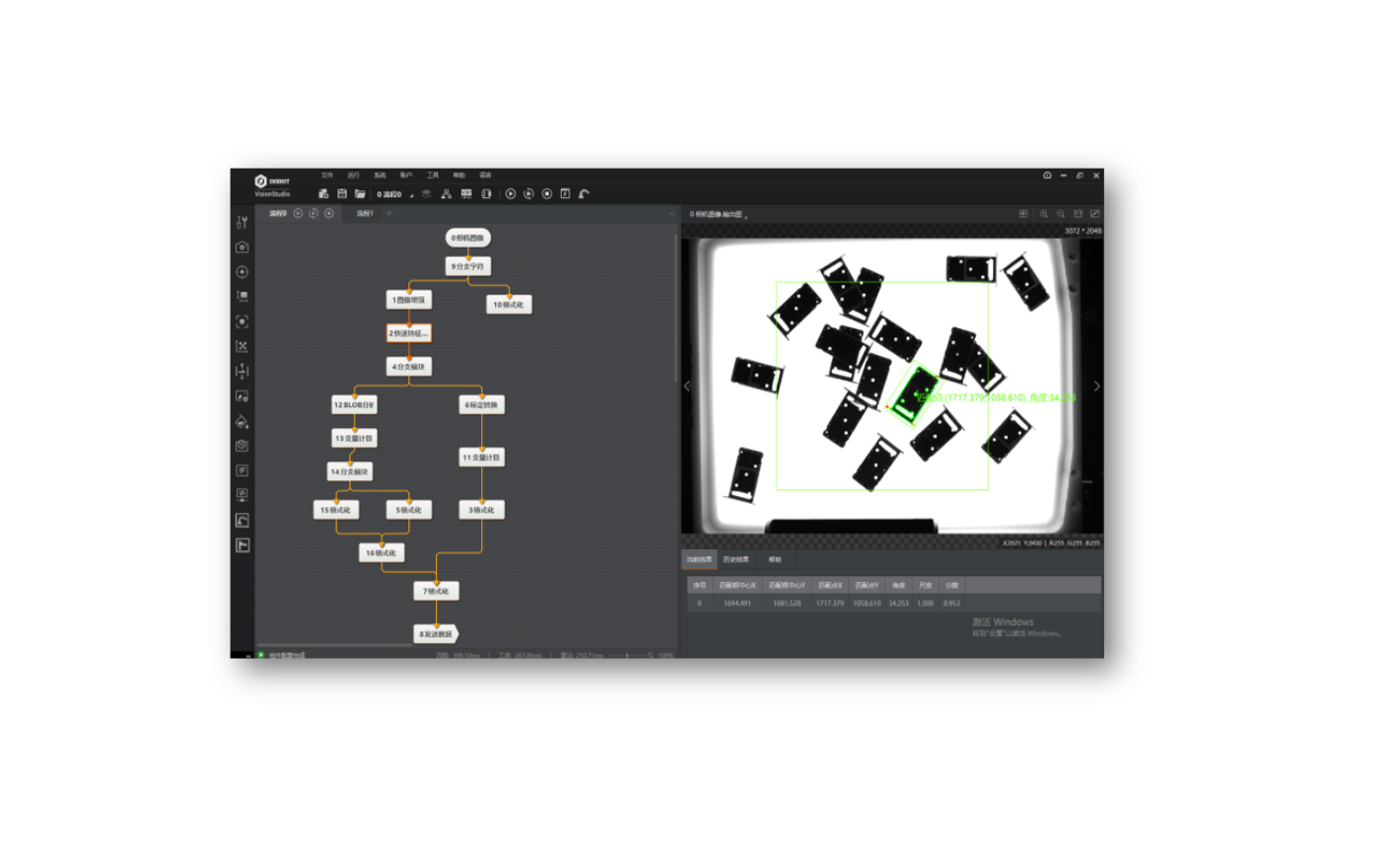
Coordinate systems
The coordinate system of the robotic arm system is divided into four coordinate systems:
Base coordinate system: the base coordinate system defines the coordinates, position and motion of the end tool, based on the base coordinate system, which is defined by the Cartesian coordinate system.
Joint coordinate system: The hinge coordinate system is defined by the possible movements of each hinge
End-tool coordinate system: Coordinate system defining the offset distance and rotation angle, whose origin and orientations vary depending on the position of the workpiece on the robot table
User Coordinate System: A movable coordinate system used to represent equipment such as fixtures, workbenches. The orientation of the origin and axes can be determined based on site requirements, to measure point data within the work area and to conveniently arrange tasks.
Singularity points
When the robot is moving in the Cartesian coordinate system, the resulting velocity of the two axes cannot be in either direction if the directions are in line, which results in the robot's degrees of freedom being degraded. The robot has three singularity points.
Safe investment, outstanding reliability
The robust and stable build quality of the CR series of collaborative robot arms promises a lifetime of up to 32,000 hours, combined with low running costs. This makes the CR series not only a safe investment, but also a return on investment.