Collaborative Industrial Robotic Arm
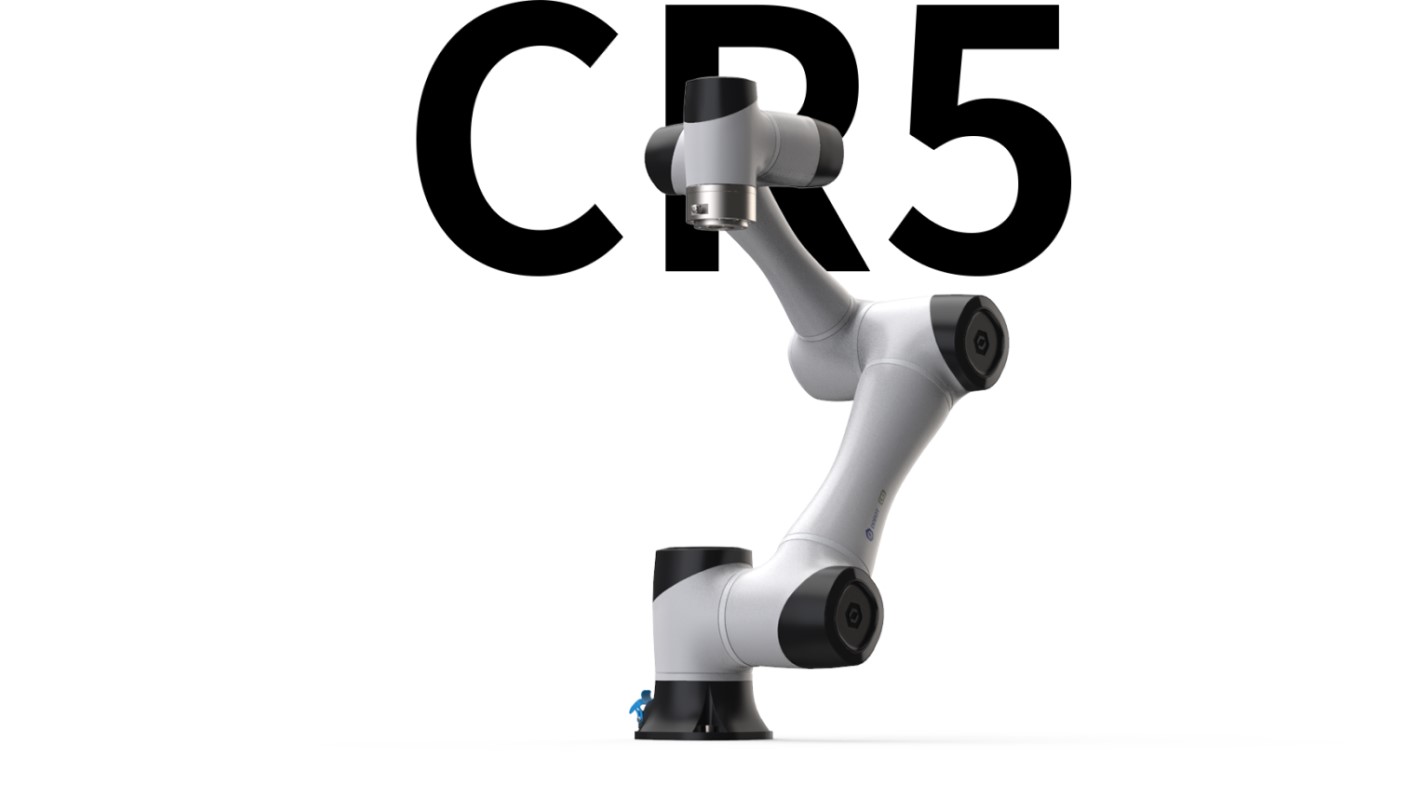
The Dobot CR5 belongs to the medium size class of industrial cobots, its compact size and 5kg load capacity allow a wide range of production automation with the robotic arm. It is available with a wide range of end tools and applications, making it an extremely useful tool for all areas of industry. It is also an excellent tool for vocational training, higher education, warehousing, production simulation and many other applications.
FLEXIBLE INSTALLATION, FAST IMPLEMENTATION
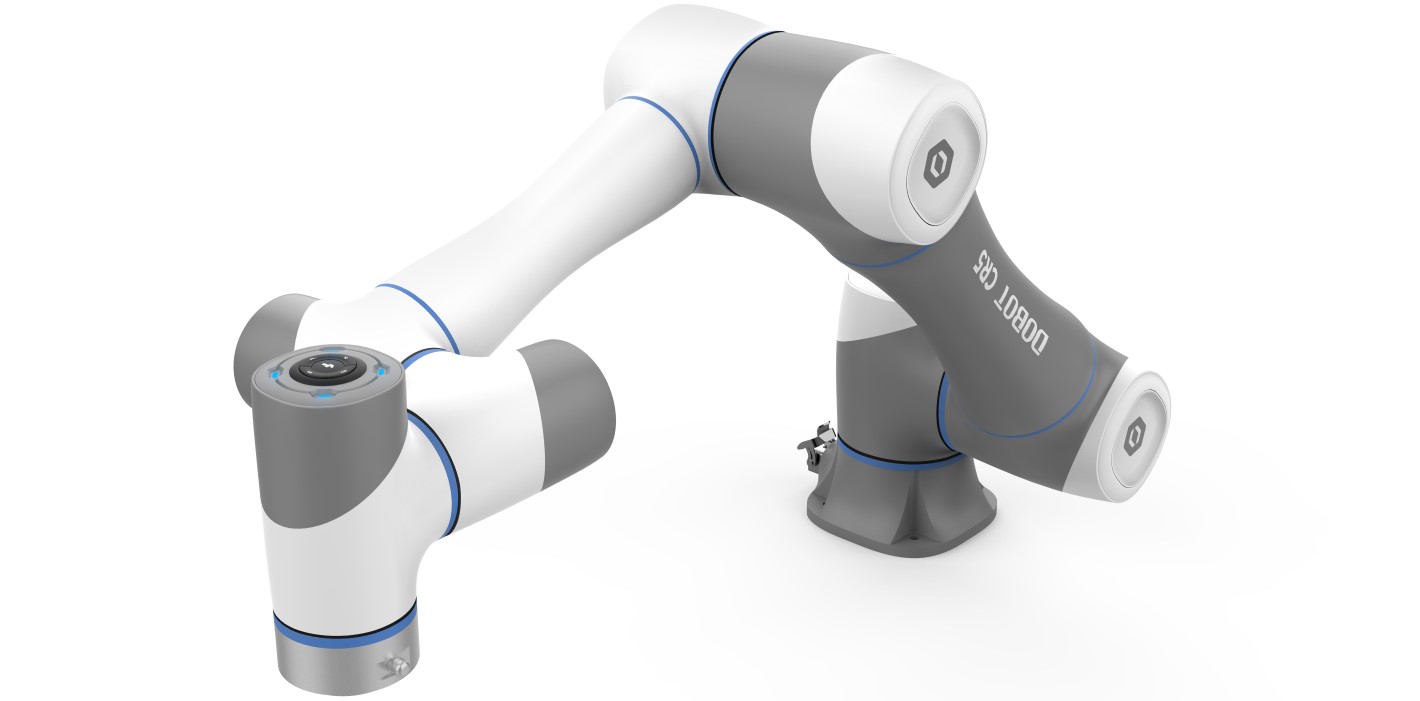
Improve workflow flexibility and production efficiency with an easy-to-deploy CR collaborative robot that can be set up in just 20 minutes and up and running in up to 1 hour. After connecting the control console and attaching the robot arm, all you need to do is connect the two devices and switch on the system.
EASY TO ACCESS, EASY TO LEARN
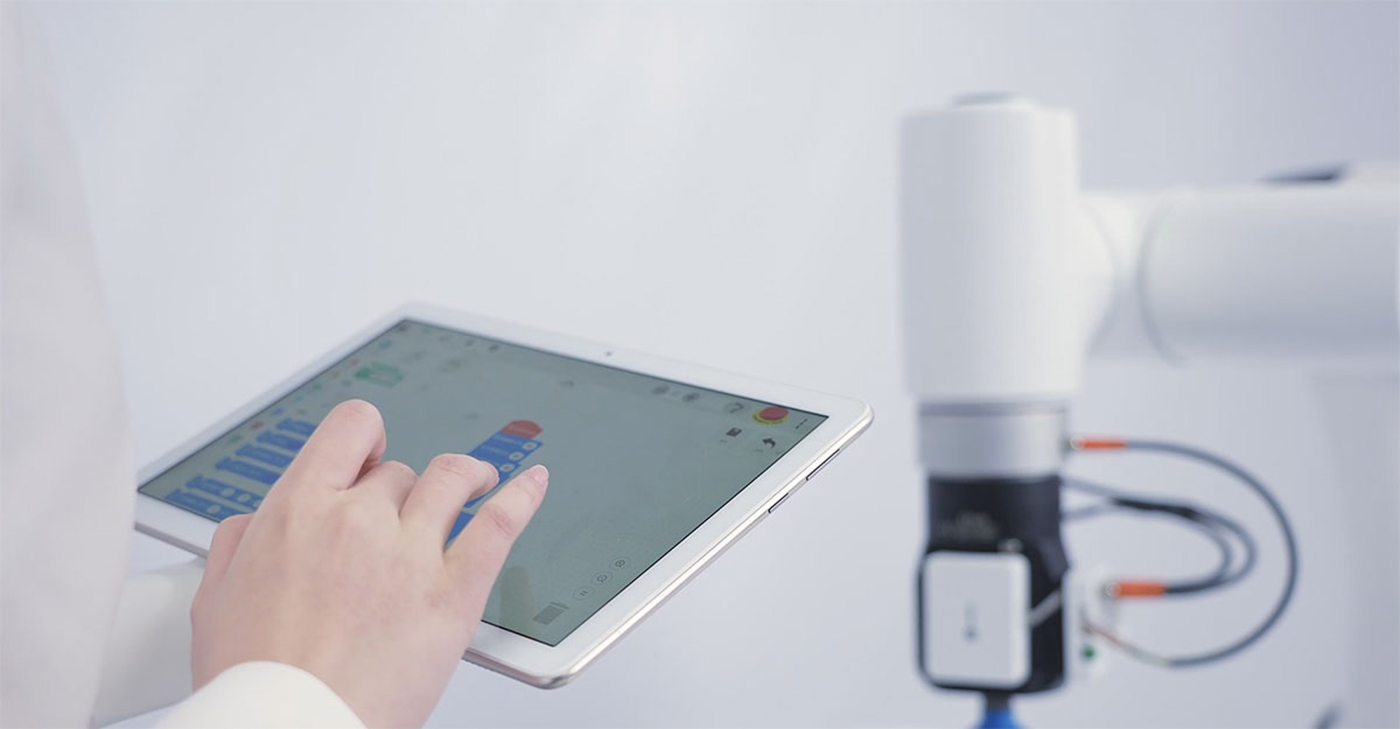
Dobot's software and arithmetic technology make the CR series of collaborative robots smart and easy to operate and manage. Thanks to software and manual training, it can accurately mimic human movements. No programming skills are required. This is facilitated by its block-based development environment, which eliminates the need to learn to use complex programming library systems and functions.
In case you have prior programming knowledge, the robot system supports the Python programming language, so you can take full advantage of the robot.
Advanced security system and more
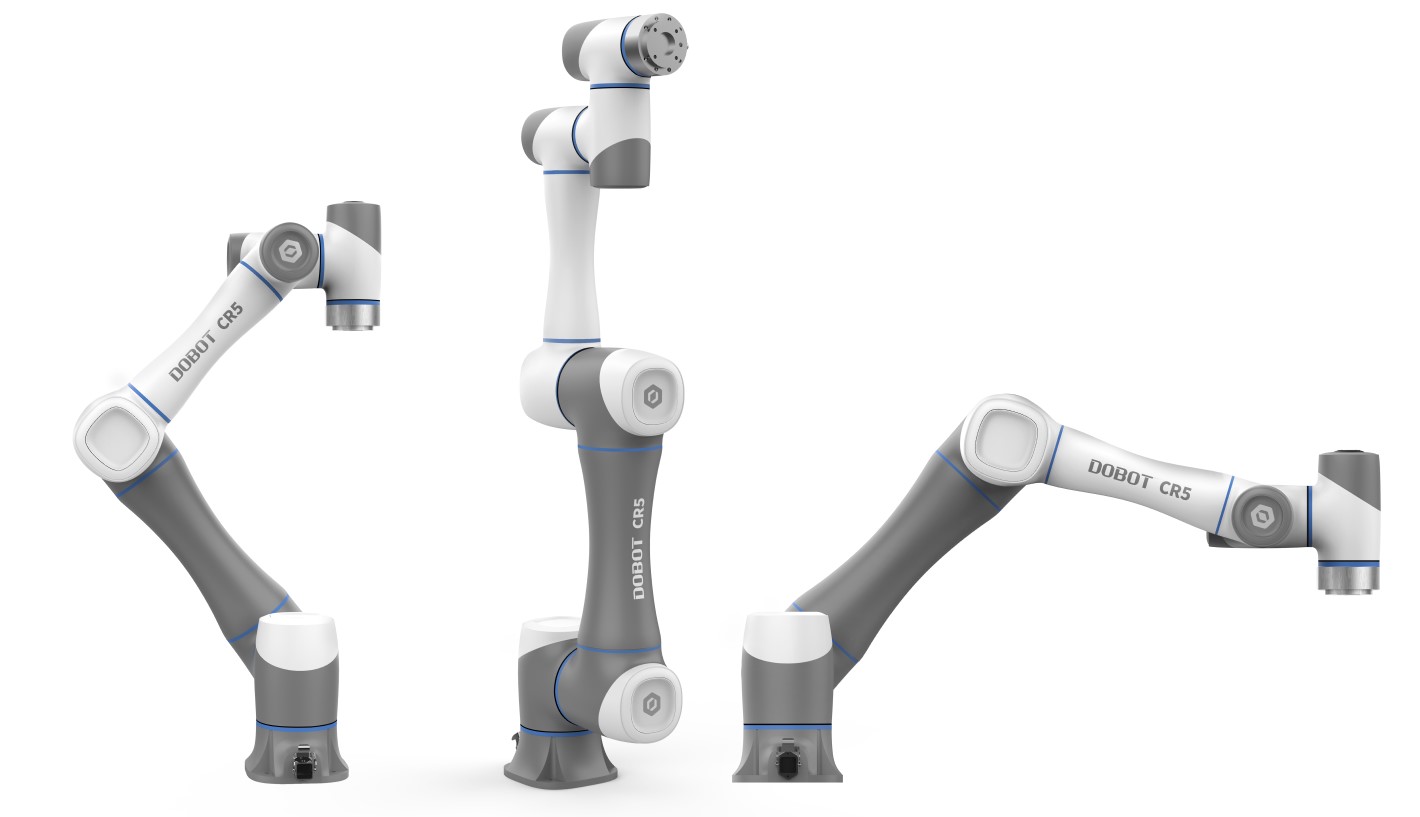
The advantage of collaborative robots is that they are equipped with pressure sensors in their enclosures, so that if the pressure exceeds a threshold, the robot stops its current work and the system does not continue until the pressure is released. With this addition, the efficiency and safety of human-robot work is taken to new levels.
Expandable, compatible
The CR collaborative robot series is also recommended for its universal communication interfaces, in addition to its wide range of end tools. Featuring multiple I/O and communication interfaces, the CR cobot series is widely expandable and compatible with a wide range of end-of-arm tools. As a result, CR cobots can meet a wide range of needs and can be used in a variety of application situations.
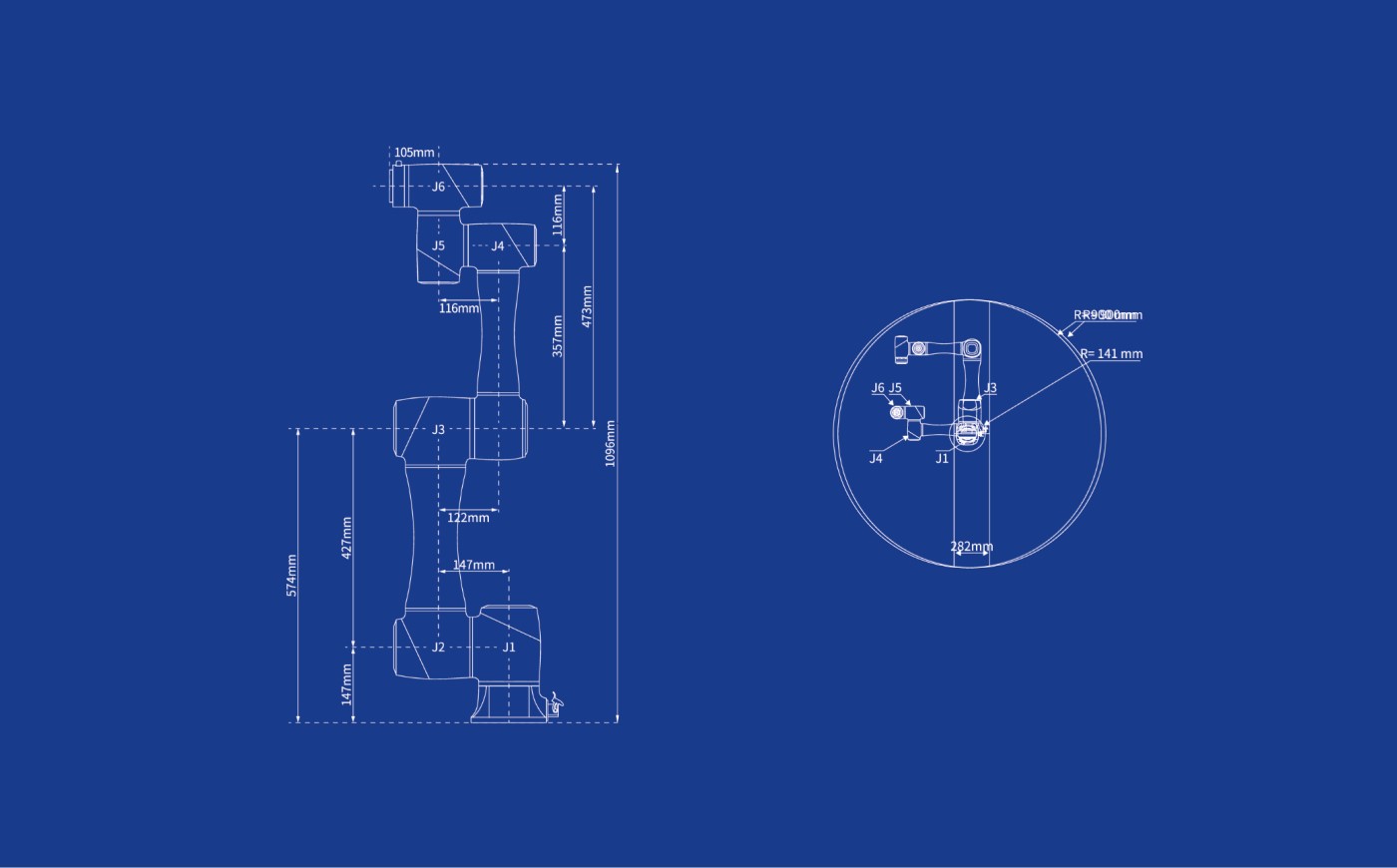
Safe investment, outstanding reliability
The robust and stable build quality of the CR series of collaborative robotic arms promises a lifetime of up to 32,000 hours, combined with low running costs, making the CR series not only a safe investment, but also a return on investment.
Parameters
|
Weight | 25kg |
Max workload | 5kg |
Max working radius | 1096mm |
Rated Voltage | DC48V |
Max speed of TCP (End Tool) | 3m/s |
Freedom of joints | J1 | ±360° |
J2 | ±360° |
J3 | ±160° |
J4 | ±360° |
J5 | ±360° |
J6 | ±360° |
Max speed of joints | J1/J2 | 180°/s |
J3/J4/J5/J6 | 180°/s |
Robot arm end IO interface | DI/DO/AI | 2 |
AO | 0 |
Communication interface | Communication | RS485 |
Controller I/O | DI | 16 |
DO/DI | 16 |
AI/AO | 2 |
ABZ Incremental Encoder | 1 |
Repeated accuracy | ±0.02mm |
Communication | TCP/IP, Modbus, EtherCAT,WIFI |
IP rating | IP54 |
Working temperature | 0~45° |
Power | 150W |
Materials | Aluminum alloy, ABS plastic |
End Tools
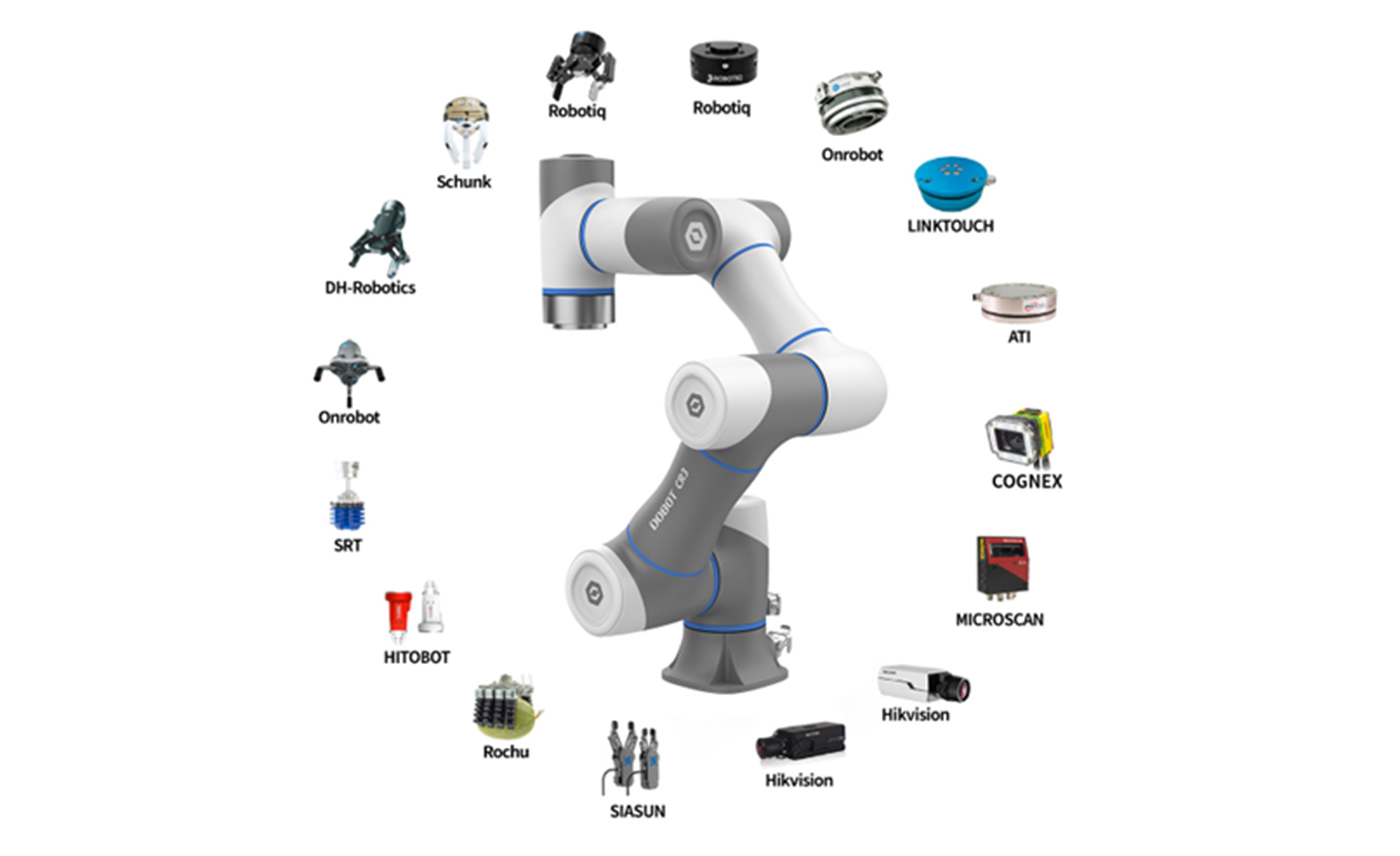
The end tools are the devices that can be mounted on the ends of the robot arms. The DOBOT CR collaborative robot series is compatible with a wide range of end tools, so it will be able to meet even the most specific needs of your business.
- Packing and palletising
- Handling
- Polishing
- Screwing
- Gluing, batching and welding
- Assembly
- Machining
- CNC
- Quality control
- Injection moulding
Content of package
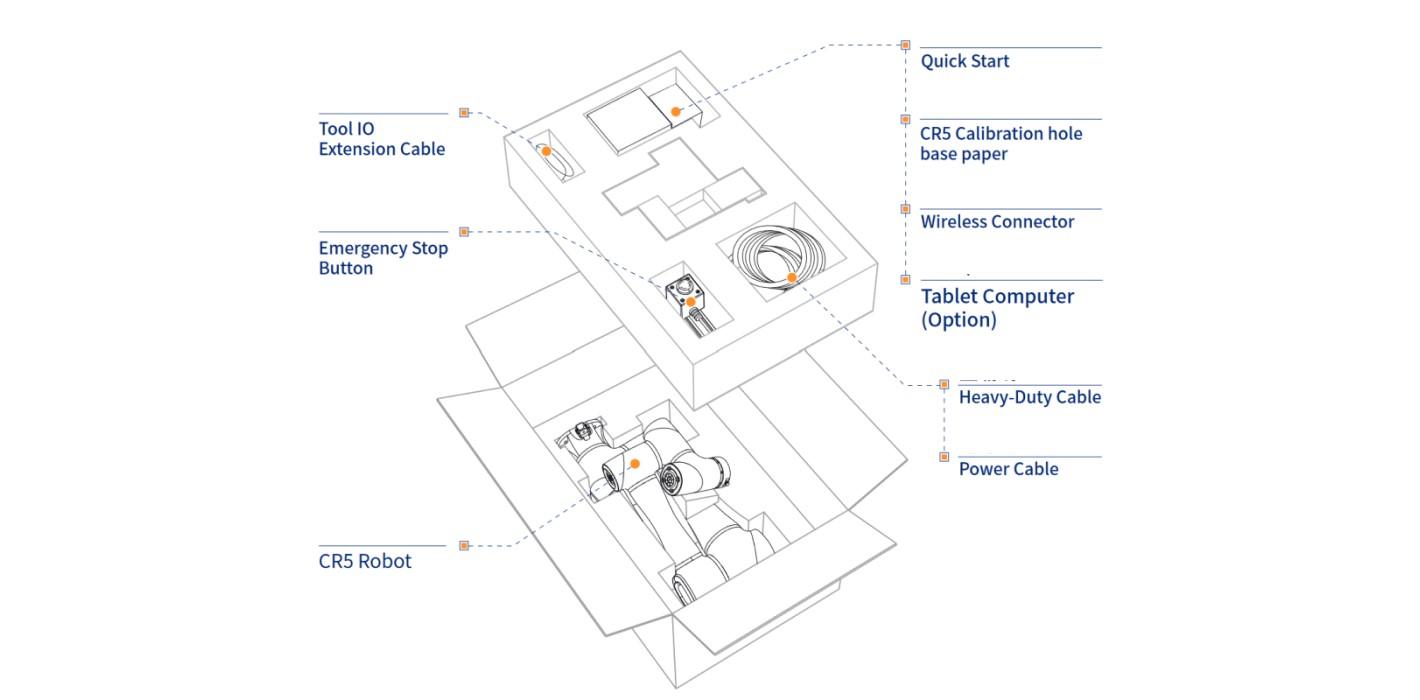
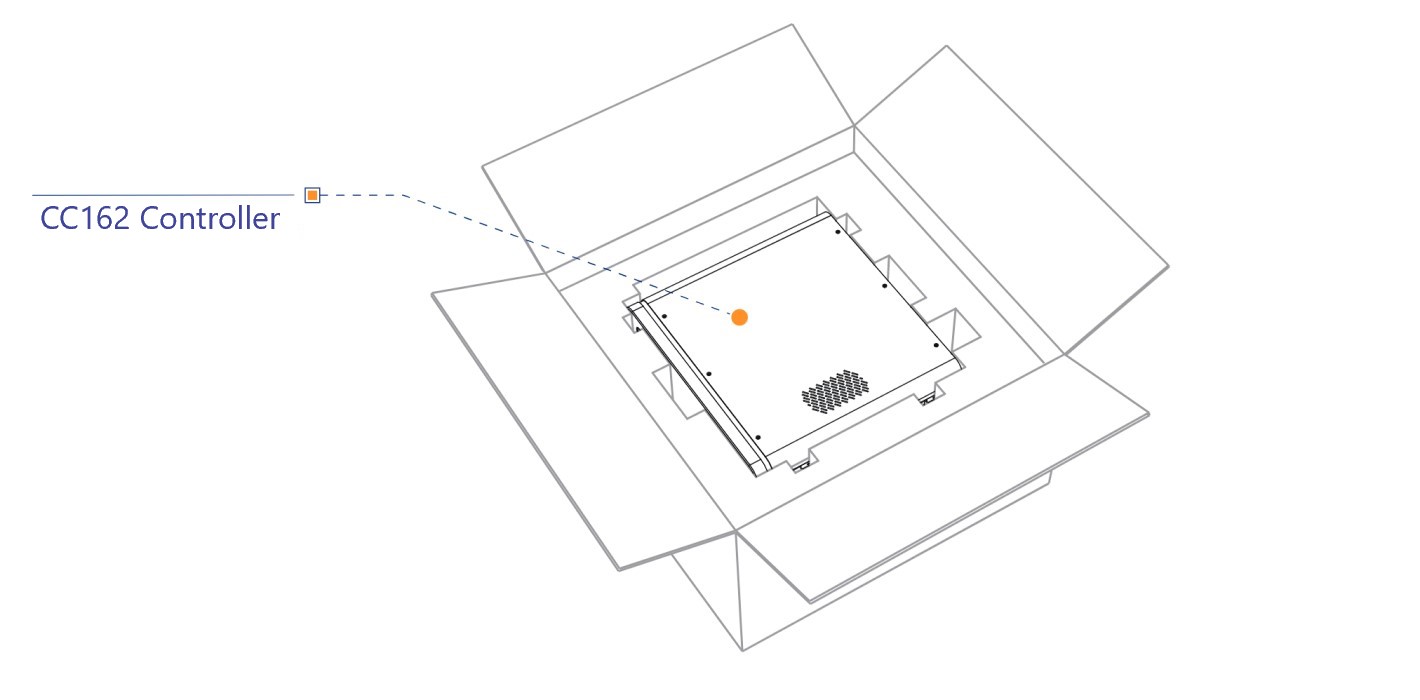
The robot arm consists of two units. A robot arm and a control unit for programming it. The control unit is a computer that contains the development environment of the robot arm. The controller has the IO ports to which the various accessories can be connected, including the emergency stop switch
* Pressing the emergency stop switch will stop the robot immediately.
In addition to the two units, the package includes the power cables for the units and the IO cable for connection.
*The robot arm is also available with an enhanced safety system, which includes a silicon-based outer casing that allows the robot arm to stop working when it is close to a foreign object, thus preventing accidents from occurring and not preventing them.
6 axes, 4 movement modes
The robot arm can move from point A to point B by connecting two coordinate points in 3 modes:
Joint Interpolated Motion: the motion can be implemented using GO and MoveJ software, which allows the robot arm to reposition from point A to point B by interpolating the joint angle of the robot arm without taking into account the position of the end tool
Linearly Interpolated Motion: The motion can be implemented by Move, which allows the robot to link the coordinates of point A and point B, looking at the position of the sky, which guides the end tool in a straight line. In the case of linear motion, a distinction can be made between the use of the jump mode, where the end tool either moves the two coordinate points to their end positions or applies a rounding off to the coordinates of the point to perform a continuous motion.
ARC -Circular Interpolated Motion: The robot connects points A and B along an arc by means of an auxiliary point C, thus performing an arc motion taking into account the position of the end tool
Circle - Circular Interpolated Motion: The robot connects points A and B by means of a helper point C and performs its motion by describing a circular shape, taking into account the position of the end tool.
It can be programmed in several ways. Examples include:
Reproduction of end-tool motion: a related programming method is Teach & Playback programming, a way of programming robot arms that does not require programming knowledge to set the parameters of a task. The programmer can freely move the robot arm by pressing and holding a safety lock release button, and then release the button to stabilize the arm in the position. In the programming interface, these coordinates can be viewed and stored as a coordinate point that the robot arm must touch during the execution of a task. By saving the points, you can then move the robot arm without any programming skills.
Block-based programming (Drag and Drop): also known as graphical programming, which makes it easier to learn programming by visualising functions, variables and modes of operation. The principle of operation is based on the linking of blocks, i.e. the blocks representing each function can be programmed in sequence to program the robot arm.
Python Script: Because of its easy-to-understand syntax and its huge library, it is used not only for automation but also for building artificial intelligence. Thus, robotics has also chosen Python to maximise the capabilities of robots. DobotCRStudio, the development environment for the robot arm, comes with the libraries needed to control the robot arm by default, so all you have to do is review the documentation and create your own Python program to run your robot arm.
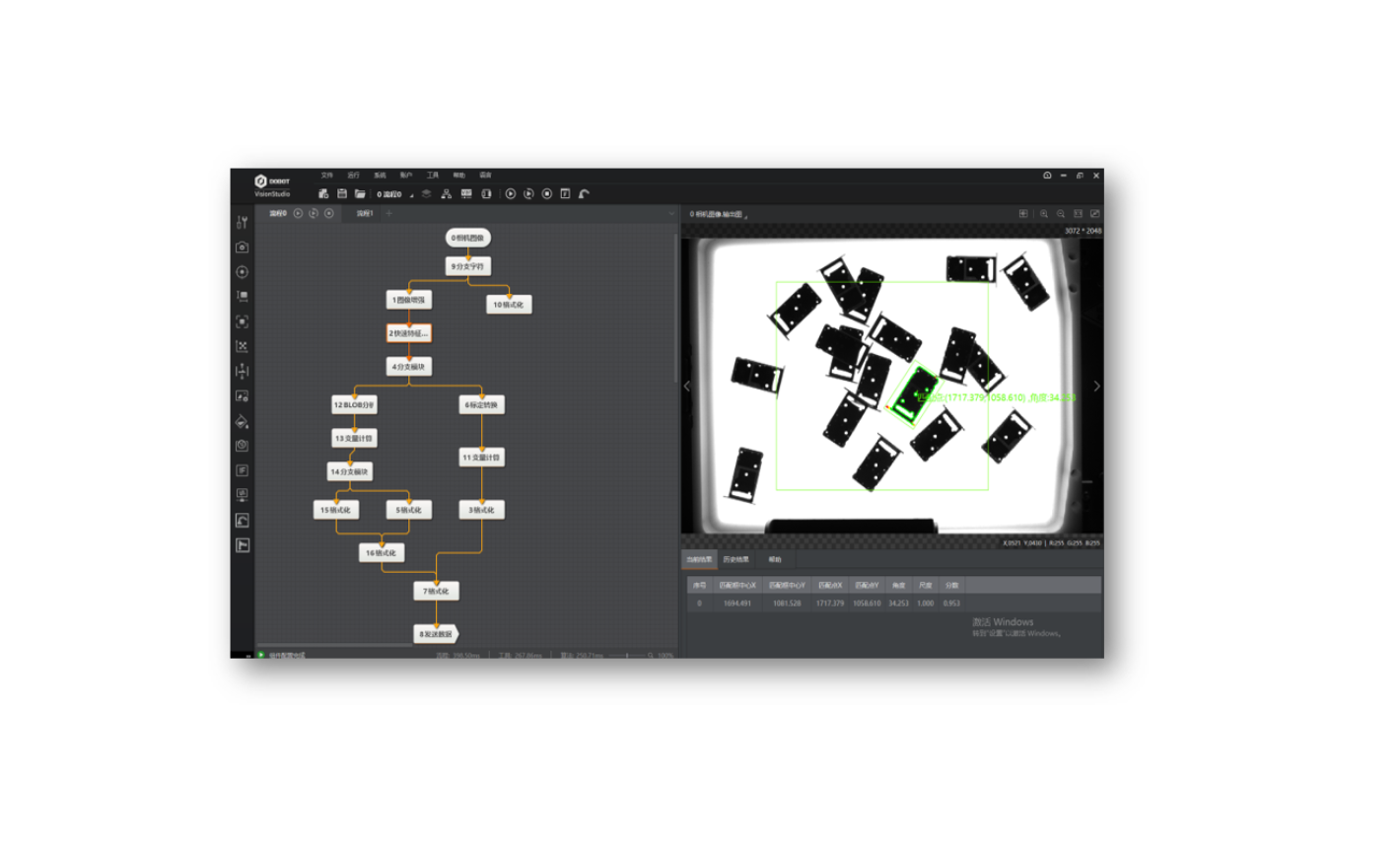
Coordinate systems
The coordinate system of the robotic arm system is divided into four coordinate systems:
Base coordinate system: the base coordinate system defines the coordinates, position and motion of the end tool, based on the base coordinate system, which is defined by the Cartesian coordinate system.
Joint coordinate system: The hinge coordinate system is defined by the possible movements of each hinge
End-tool coordinate system: Coordinate system defining the offset distance and rotation angle, whose origin and orientations vary depending on the position of the workpiece on the robot table
User Coordinate System: A movable coordinate system used to represent equipment such as fixtures, workbenches. The orientation of the origin and axes can be determined based on site requirements, to measure point data within the work area and to conveniently arrange tasks.
Singularity points
When the robot is moving in the Cartesian coordinate system, the resultant velocity of the two axes cannot be in either direction if the directions are aligned, resulting in the robot's degrees of freedom being degraded.
The robot has three singularity points.
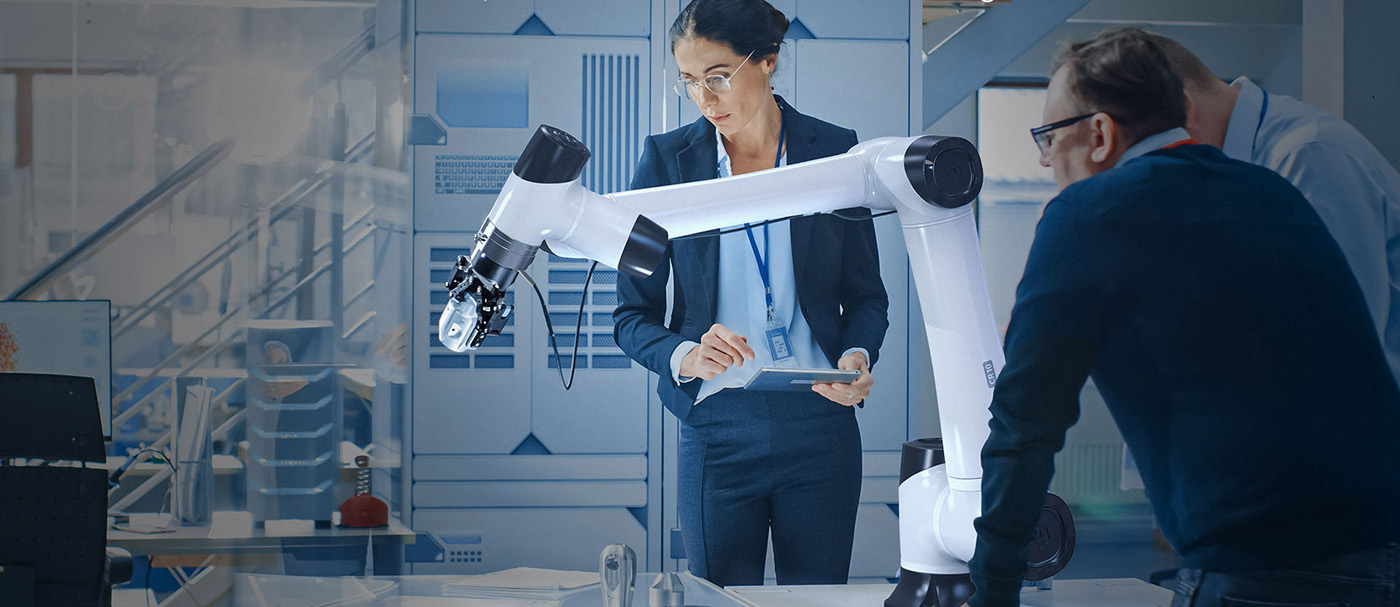